Bespoke Equipment Maintenance Software
What is Facility Equipment Maintenance System?
Facility equipment maintenance system is a category of software that enables businesses to track and manage their equipment maintenance activities. These systems are designed to help organizations manage maintenance tasks for their equipment, ensuring that it operates at peak performance levels.Contact us if you are wanting to have a bespoke Equipment Maintenance application developed?
The primary purpose of a facility equipment maintenance system is to help businesses reduce downtime and increase efficiency by streamlining maintenance processes. These systems enable businesses to proactively schedule maintenance activities, monitor equipment performance, and identify potential problems before they turn into major issues.
Depending on the specific needs of a business, facility equipment maintenance systems can include a range of features and capabilities. Some of the most common functions of these systems include preventative maintenance scheduling, work order management, equipment inventory tracking, and reporting and analytics.
In addition to these core features, some facility equipment maintenance systems may also include advanced capabilities such as asset tracking and management, predictive maintenance, and mobile access. These features can help businesses optimize their maintenance workflows and improve equipment performance even further.
Overall, a custom facility equipment maintenance system can be a valuable investment for businesses looking to improve their maintenance operations and maximize equipment uptime. By automating maintenance processes and providing real-time insights into equipment performance, these systems can help businesses save time, reduce costs, and increase productivity.
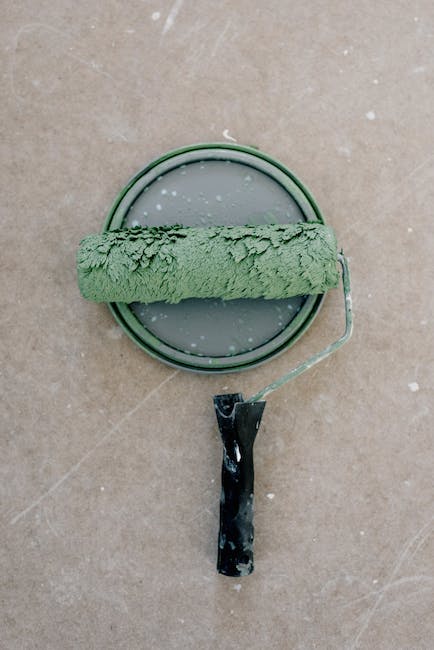
What are the main functions of Facility Equipment Maintenance System?
One of the key modules of a facility equipment maintenance system is asset management. This module is responsible for tracking and managing all equipment within a facility, including its location, maintenance history, and current condition. It allows businesses to keep accurate records of their equipment and make informed decisions about maintenance schedules and replacement.Another important module is preventive maintenance, which sets up automated schedules for routine maintenance tasks, such as oil changes or equipment inspections. This module helps prevent breakdowns and extends the lifespan of equipment, saving businesses money in the long run.
A work order module is also essential, allowing employees to easily create and manage work orders for equipment maintenance or repair. It provides a centralized location for assigning tasks, tracking progress, and closing out work orders.
Other common modules include inventory management, which tracks parts and supplies needed for maintenance or repair, and a reporting module that provides insights into equipment maintenance trends and costs.
Overall, a facility equipment maintenance system provides businesses with a comprehensive solution for managing their equipment, ensuring it is running at optimal levels and reducing the risk of costly breakdowns or downtime.
Data / systems integration
Facility equipment maintenance systems are often integrated with other systems in order to improve the overall efficiency of facility management. Some common systems that facility equipment maintenance systems are integrated with include ERP (Enterprise Resource Planning), CMMS (Computerized Maintenance Management System), EAM (Enterprise Asset Management), and SCADA (Supervisory Control and Data Acquisition) systems.APIs (Application Programming Interfaces) or other tools are often used for this integration. APIs allow for seamless communication between two different systems and can streamline the transfer of data. When selecting an API for integration, it is important to consider factors such as the compatibility of the two systems, the security of the API, and the ease of implementation.
Another consideration when integrating facility equipment maintenance systems with other systems is the type of data that will be shared. It is important to ensure that the data is accurate and up-to-date, as well as secure. Additionally, it is important to consider any regulations or compliance requirements that may impact the sharing of data between systems.
Overall, integrating facility equipment maintenance systems with other systems can provide numerous benefits including increased efficiency, improved data accuracy, and better overall facility management. Careful consideration of the tools used for integration and the type of data shared can help ensure a successful and secure integration.
Who uses Facility Equipment Maintenance System?
Organizations across various markets and verticals use facility equipment maintenance systems and equipment management software. These systems are particularly useful for companies that operate in industrial sectors such as manufacturing, construction, transportation, and logistics, where maintaining and servicing equipment is a critical component of their business operations. However, they are also used by other organizations that need to manage a large number of assets or equipment, such as hospitals, universities, hotels and resorts, shopping malls, and sports facilities. The size of the organization that uses these systems varies widely, ranging from small businesses to large multinational corporations with complex equipment management needs.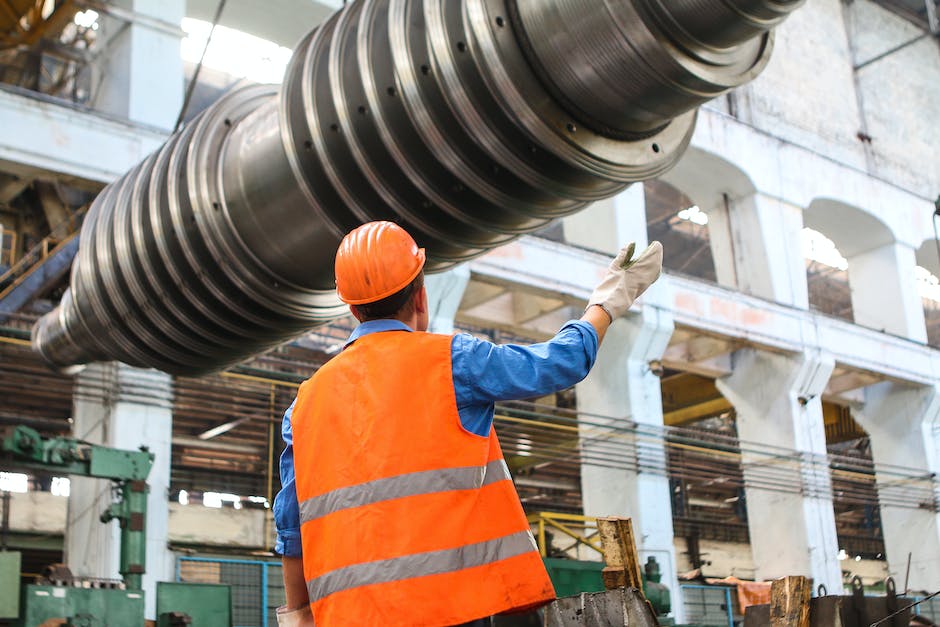
Benefits of Facility Equipment Maintenance System
Organizations use facility equipment maintenance systems to streamline and improve their maintenance processes. By automating the tracking of equipment maintenance schedules, work order management and inventory control, businesses can enhance their productivity and reduce downtime. The key benefits of using a facility equipment maintenance system include increased equipment reliability, improved asset utilization, lower maintenance costs, and enhanced regulatory compliance. Additionally, facility equipment maintenance systems provide real-time visibility into equipment performance, enabling businesses to identify issues early and take proactive steps to maintain and improve equipment performance. Overall, with the help of a custom facility equipment maintenance system, businesses can improve the performance of their equipment, reduce overall maintenance costs and create a more efficient maintenance process that ultimately benefits their bottom line.Some of the players in the Facility Equipment Maintenance System market
Some of the main brands of facility equipment maintenance system, equipment management software include:1. IBM Maximo: IBM Maximo is a highly customizable software that allows the management of assets, work orders, and inventory in real-time. Its key benefits include advanced predictive maintenance capabilities and user-defined location, asset, and maintenance hierarchies. However, some customers have complained about the steep learning curve and the need for extensive training.
2. Fiix: Fiix is a user-friendly software that streamlines maintenance workflows and automates tasks. Its key benefits include seamless integration with existing systems and customizable dashboards. However, some customers have reported issues with the mobile app and the lack of advanced reporting features.
3. Hippo CMMS: Hippo CMMS is a cloud-based software that is ideal for small to medium-sized businesses. Its key benefits include an intuitive interface and robust reporting features. However, some customers have complained about the slow loading times and limited customization options.
4. eMaint CMMS: eMaint CMMS is a flexible software that can be configured to meet the specific needs of different industries. Its key benefits include easy-to-use mobile apps and a comprehensive asset hierarchy. However, some customers have reported issues with the reliability of the software and the lack of integration with third-party systems.
5. UpKeep: UpKeep is a modern, mobile-first maintenance software that allows technicians to easily submit and track work orders. Its key benefits include a simple interface and affordable pricing. However, some customers have complained about the limited functionality of the reporting features and the lack of customization options.
Benefits of off-the-shelf Facility Equipment Maintenance System
Off-the-shelf facility equipment maintenance systems have several benefits for business owners, including:1. Cost-effectiveness: Off-the-shelf systems are generally less expensive than custom systems since they are created for broader usage by multiple organizations.
2. Ease of implementation: Since these systems are already developed, they take less time to implement, and you can start using them right away.
3. Well-tested: Off-the-shelf systems are tested across various businesses, which means vendors identify any issues that may arise or problems that may be common to a particular business.
4. Scalability: As your business grows, you can easily upgrade the system and add new features, without having to start from ground zero.
5. Comprehensive: Vendors design off-the-shelf systems to offer a wide range of features and multiple solutions to meet specific business needs.
6. Support: With off-the-shelf systems, you usually have access to vendor support and constant updates to the software to ensure it remains relevant and up to date.
In conclusion, while custom facility equipment maintenance systems offer specific additional advantages, off-the-shelf systems can also prove highly beneficial for businesses looking for an economical, easy-to-deploy, and feature-rich solution.
Limitations of off-the-shelf Facility Equipment Maintenance System
Off-the-shelf facility equipment maintenance systems, while widely available, come with their own set of limitations. These limitations can affect the overall effectiveness of the system and limit the ability to customize it to specific needs. Here are some examples of the limitations of off-the-shelf facility equipment maintenance systems:1. Limited functionality: Most off-the-shelf solutions offer a set of basic features that may not be sufficient for all types of businesses. For instance, a manufacturing firm may have unique equipment maintenance needs that can only be met with a custom solution. Pre-built software may not offer enough flexibility to accommodate these types of specialized requirements.
2. Lack of scalability: Many off-the-shelf maintenance systems come with pre-determined limits on the number of users, equipment or sites that can be managed. As your business grows, you may need to add users, equipment or sites - and if your system is not scalable, you may have to switch to another solution that can meet those growing needs.
3. Lack of flexibility: Your company may have specific requirements when it comes to how data is stored or how processes are automated. Off-the-shelf software may not allow for tweaks and changes to meet these unique demands. In contrast, a custom-designed system can be created to suit your exact needs.
4. Hidden costs: Often, pre-built software can be advertised as a cost-effective solution. However, hidden costs can arise when you need additional features or customizations. Some vendors may charge for support or maintenance and updates, and these can mount up over time. With a custom solution, all costs are upfront, and you only pay for what you need.
5. Training: Employees who have used a particular facility equipment maintenance system over many years become comfortable with its interface and features. With off-the-shelf software, there may be a learning curve involved when the new system is installed and people will have to spend time training and adapting.
To summarize, while off-the-shelf maintenance solutions may suit some businesses, it's important to be aware of their limitations. Through the development of a custom facility equipment maintenance system, businesses can create a solution that addresses their specific needs and requirements.
Is bespoke Facility Equipment Maintenance System a viable option?
Bespoke or partially bespoke facility equipment maintenance systems are tailored specifically to a business's unique needs and requirements. These custom systems offer several benefits over off-the-shelf software solutions.One of the most significant advantages of a bespoke facility equipment maintenance system is that it can be designed to integrate seamlessly with the business's existing processes, procedures, and systems. This integration means that the new maintenance system can be deployed and adopted without causing any significant disruption to the business's operations.
Furthermore, a bespoke system is developed based on the business's specific needs, which means that the software is designed to solve the specific challenges the business faces. It is developed in close collaboration with the business's team, ensuring that it meets their exact requirements. This personalized approach enhances user adoption, increases efficiency and reduces downtime.
Bespoke facility equipment maintenance systems are often built with scalability in mind. They are designed to grow and adapt as the business's needs change over time, making them a long-term investment.
Successful use cases of a custom facility equipment maintenance system include a large-scale manufacturing company that required predictive maintenance, quality control and data analysis features. The result was an increase in efficiency, a decrease in downtime, and considerable cost savings. Another example is a warehousing and distribution company that required a solution to automate their equipment maintenance tasks, resulting in better time management, reduced downtime, and organized record-keeping.
In conclusion, bespoke or partially bespoke facility equipment maintenance systems offer a range of benefits to businesses, including seamless integration, solving specific challenges, scalability, and long-term investment. These custom systems have proved their worth in various industries, resulting in increased efficiency, cost savings, and improved user adoption.
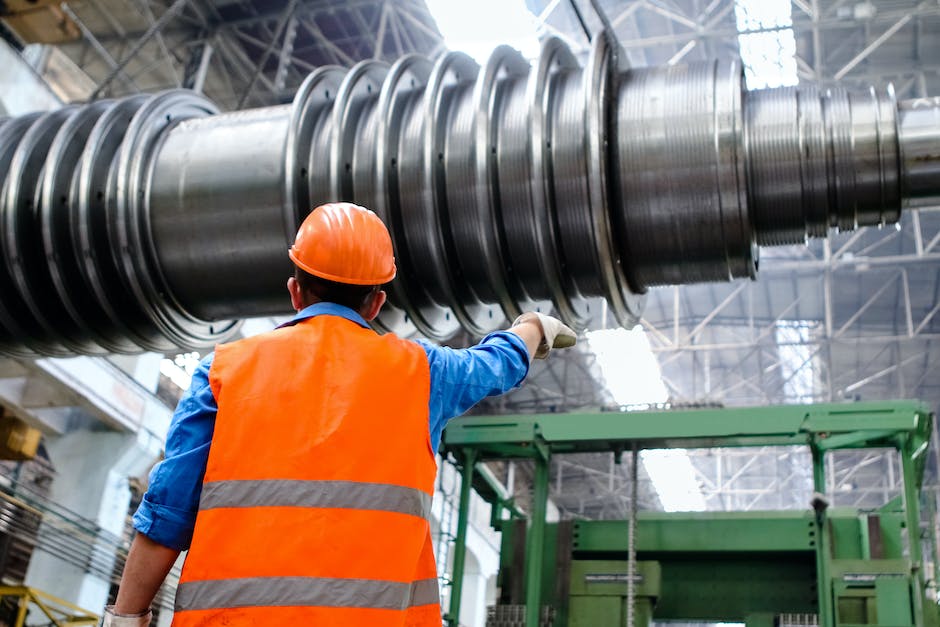
Fun facts about Facility Equipment Maintenance System
- According to a report by Grand View Research, the global facility management market is expected to reach USD 83.61 billion by 2025 with a CAGR of 12.9%.- The use of equipment management software can reduce downtime by up to 40%, resulting in increased productivity.
- A survey by Jones Lang LaSalle found that 79% of facility managers believe that implementing a computerized maintenance management system (CMMS) improves maintenance operations.
- Equipment management software can help businesses save money by reducing labor costs and minimizing the risk of breakdowns and repairs.
- Predictive maintenance is a growing trend in equipment management software, allowing businesses to identify potential breakdowns before they occur and schedule maintenance accordingly.
- Mobile accessibility is becoming increasingly important in facility equipment maintenance systems, allowing technicians to access information and perform tasks from anywhere.
- Integration with other systems, such as building automation and energy management systems, can provide a more holistic solution for facility management.
- Equipment management software can also help businesses stay compliant with industry regulations and standards.
Facility Equipment Maintenance System FAQ
1. What are the benefits of having a custom facility equipment maintenance system developed for my business?A custom facility equipment maintenance system can provide numerous benefits for your business, such as streamlining maintenance processes, improving equipment uptime, reducing downtime and maintenance costs, enhancing asset tracking and management, providing data insights and analytics for informed decision-making, and improving overall productivity and efficiency.
2. How does a custom facility equipment maintenance system differ from off-the-shelf solutions?
A custom facility equipment maintenance system is specifically tailored to meet the unique needs and requirements of your business, equipment, and maintenance processes. Off-the-shelf solutions may not have all the functions or features you require, whereas a custom solution can be created to include exactly what you need.
3. What should I consider when choosing a software development company to develop my facility equipment maintenance system?
When choosing a software development company, you should consider their experience and expertise in developing facility equipment maintenance systems and equipment management software. Look for a company that has a track record of delivering high-quality custom solutions, and one that is willing to work closely with you to understand your business needs and requirements.
4. How long does it take to develop a custom facility equipment maintenance system?
The development timeline for a custom facility equipment maintenance system can vary depending on the complexity of your requirements and scope of the project. A detailed discovery and planning phase is essential to ensure that all requirements are understood, so that a realistic timeline can be developed.
5. What should I expect in terms of ongoing support and maintenance?
Ongoing support and maintenance may be included in your development contract, or it may be an additional service that is offered by the software development company. This can include regular system updates, bug fixes, and technical support, to ensure that your facility equipment maintenance system continues to function effectively.
6. How will my data be secured within the custom facility equipment maintenance system?
Data security should be a top priority when developing a facility equipment maintenance system. The software development company should have processes in place to ensure that your data is securely stored, and that access to it is restricted to authorized personnel only.
7. What are the costs involved in developing a custom facility equipment maintenance system?
The costs of developing a custom facility equipment maintenance system can vary depending on the complexity of your requirements and the scope of the project. A detailed discovery and planning phase is essential to establish a realistic budget and ensure that all costs are accounted for.
Next Steps?
Are you tired of managing your equipment maintenance manually? Do you wish you could access all your equipment data with just a simple click? Look no further! Our bespoke facility equipment maintenance system is your solution. With our expertise in equipment management software, we can design a custom system tailored to your needs.Why settle for generic systems that won't fully meet your equipment maintenance requirements? Our team of experts will work closely with you to identify your specific needs and develop a system that will streamline your equipment maintenance processes. Our attention to detail and understanding of the equipment maintenance industry ensures that you will end up with a system that is efficient, reliable and easy to manage.
You can trust us for all your systems integration and data migration needs too. With our experience and meticulous approach, we can ensure a seamless transition from your current system to your new bespoke facility equipment maintenance system. We will also provide you with training to ensure that you and your team can fully utilize your new system and maximize its potential.
Don't let equipment maintenance be a headache for your business any longer. Contact us today and let us develop a custom facility equipment maintenance system that meets all your needs. Your equipment (and your sanity!) will thank you for it.
Read more about the main software category Utility Applications.
Other services in Utility Applications category:
Want a quick quote for the development of custom Equipment Maintenance Application?
Contact us to discuss your questions about bespoke Equipment Maintenance Applications.